Amparo Vázquez: "After a year of research and hard work, we now consider ourselves plastronics integrators"
The aim was to truly take up the challenge and experiment with in-mould electronics, using a part that was as difficult as it could be: capacitive sensors, lighting, dimmer... all within a minimum thickness and in a curved part. Was it a crazy thing to try and do? No: it was a way for Industrias Alegre's R&D&I department to test our capabilities and put ourselves through a tough apprenticeship. Now, a year later and with the team feeling confident about this emerging technology, we talk about the experience gained with the head of the department, Amparo Vázquez.
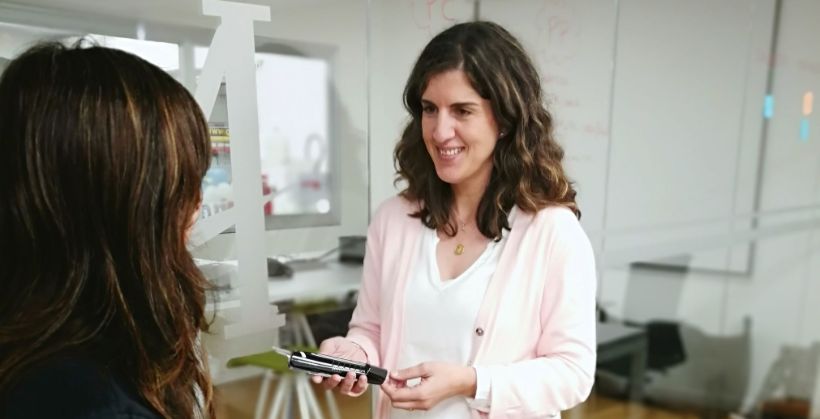
Why integrate In-Mould Electronics technology into Industrias Alegre's portfolio of services?
Because innovation is in our company's DNA and because the business strategy that directs our decisions is centred around adding value for our customers. We need to anticipate the needs of the industry we serve and, in our exploratory work, it was clear to us that we should have a deep understanding of in-mould electronics so that we could offer this service to our customers. It is a way of simultaneously responding to the aesthetic and design trends towards minimalism and comfort and the needs related to the electrification of cars, which requires lighter elements.
Tell us about the demonstrator that you've developed.
Together with Eurecat, we jointly developed a part that we know well: the interior column of a car. And we fitted it with capacitive switches, lighting, dimmer... It is not a real part, of course, because the column is not where switches are located (at least, they aren't currently). But we know that it is a part where it is very difficult to integrate electronics and we wanted to stretch ourselves and see if we could overcome the challenge. And yes, we succeeded. Today we have a real-life demonstrator: you can try it, touch it, see how it works.
So, the project was to challenge yourselves?
The project consisted of studying the feasibility of this type of part. We are manufacturers and we know that to take an idea from a drawing to a mass-produced part entails a series of difficulties that we can't always foresee. We're experts in the real world! When approaching a project like this - one that has a very high degree of difficulty - we wanted to work the way we do when a customer approaches us: study the part, analyse its functions, assess its geometry and take the whole assembly through to a smooth manufacturing process. The difference is that, in the middle of the process, we had to integrate the film with the functional electronics and learn to work with it.
Does this mean that you are now in a position to offer plastronics to any manufacturer?
It means that we now view ourselves as plastronics integrators. We can't do the whole process because we are experts in plastics, not electronics, so we do have to collaborate with expert partner companies. However, as far as we're concerned, we're already able to work with electronic films because we are familiar with the requirements of flexible electronics, their needs and limitations.
It sounds like it has been a year of learning...
Yes, because there are many elements involved in studying the feasibility of these pieces and drawing definitive conclusions. We're talking about geometries, mould designs, insert placement, materials and processes.
And how important was your previous experience in this process?
Our know-how built in plastic injection moulding played a definite role in tackling a part with this degree of complexity. With a large flat piece, everything would have been simpler, but we knew that moulding a structure and form like this was going to push us to the limits.
Next steps?
Although we have already proven that this is a fully viable project, we will continue to improve the demonstrator and continue building our contacts in the electronics industry in search of partnerships to help take us further.